As the e-commerce industry constantly grows, the traditional warehouse operating methods we know today struggle to keep up with the demand for speed and accuracy. Manual processes and labor shortages can lead to inefficiencies, errors, and increased costs. To combat these challenges, vision-guided robots with advanced stereo-vision cameras provide a cutting-edge solution for smarter, faster, and more accurate warehouse operations. By integrating depth perception and real-time decision-making abilities, these robots revolutionize warehouse automation and improve supply chain performance by reducing errors and improving efficiency. The main goal of this innovation is to benefit the bottom line and enhance customer satisfaction by decreasing delays in order fulfillment.
Discover the cutting-edge world of warehouse automation in this blog post, which delves into the exciting field of robotics. Explore how embedded cameras are revolutionizing warehouse operations and increasing efficiency and productivity using robots.
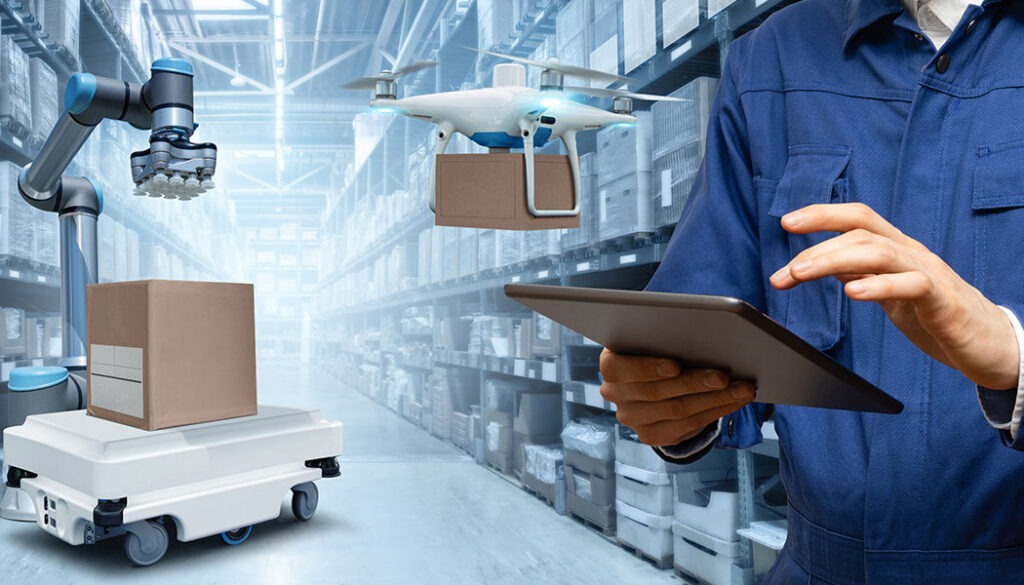
Types of warehouse robots
What is warehouse automation?
Warehouse automation is the method of incorporating automated systems, specialized software, and advanced robotics into warehouse activities to improve efficiency, accuracy, and speed in various tasks. This advanced automation transforms how materials are handled, inventory is managed, and warehouses operate, resulting in increased productivity and safety while leaving the more repetitive tasks to technology.
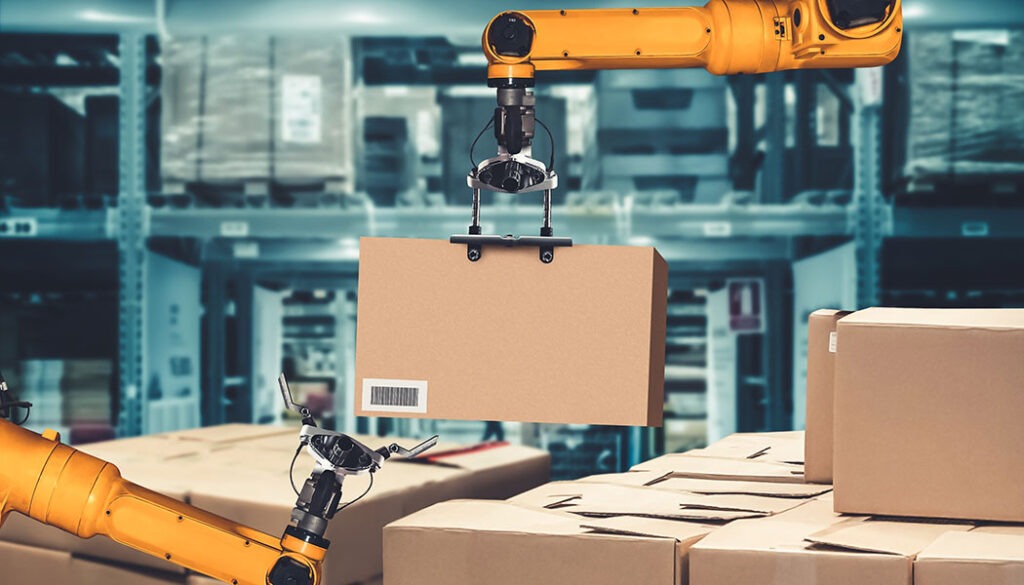
Robotic Arm
Warehouse automation comprises several key components that work together to refine operations and improve efficiency. These include automated systems such as conveyor belts, sortation systems, and automated storage and retrieval systems (AS/RS), which handle the movement and storage of goods with minimal human intervention. Specialized software like warehouse management systems (WMS) and warehouse execution systems (WES) are also crucial for coordinating activities, tracking inventory, and optimizing workflows. Robotics also plays a significant role in warehouse automation, with autonomous robots designed for specific tasks such as material transportation or inventory tracking. These robots often come equipped with advanced features such as obstacle detection sensors and stock level-based route optimization to further enhance their capabilities.
Automated systems have a wide range of applications, such as material handling, inventory management, and space optimization. These systems improve speed, accuracy, and overall efficiency by streamlining tasks such as transport, sorting, tracking, and reconfiguring warehouse layouts. They also reduce losses and improve order fulfillment rates by providing precise tracking and handling of inventory.
Benefits of warehouse robots
Robots play a key role in enhancing warehouse operations. They help automate mundane as well as intelligent tasks to free up labor time and reduce TCO (Total Cost of Ownership) for warehouse owners. In this section, let us cover the benefits of using robots in warehouses.
Enhanced worker safety: Workplace hazards associated with heavy lifting and repetitive movements are significantly reduced as warehouse robots are capable of handling heavy loads and performing tasks in high-risk zones, reducing human workers’ need to engage in potentially dangerous activities.
Improved efficiency: Workers can rapidly fulfill orders and significantly increase business productivity as robots trim the picking and packing process by swiftly transporting inventory to central locations.
Optimized storage: Certain robots are specifically designed to navigate and retrieve items from tightly packed or high shelves, areas that are typically inaccessible to human workers. This takes advantage of vertical space and tight areas.
Automated inventory management: Robots efficiently handle inventory by moving products from storage to picking areas, ensuring that picking locations remain well-stocked and worker downtime is minimized to maintain a consistent workflow.
Competitive recruitment: Warehouses equipped with cutting-edge robotics and modern technology infrastructure can attract skilled workers who are interested in working within an automated and innovative environment.
Enhanced inventory control: Robotics technology contributes to more accurate tracking and management of inventory, maintaining optimal stock levels, and preventing both excess stock and stockouts, which can be costly for businesses.
Types of warehouse robots
Warehouse robotics includes diverse robots, each serving a specific purpose in warehouse operations. These robots include Automated Guided Vehicles (AGVs), which use embedded markers or LiDAR to replace traditional forklifts and carts, improving material movement efficiency. Autonomous Mobile Robots (AMRs), utilizing sensors like LiDAR, cameras, and proximity sensors to navigate, create their own routes and intelligently avoid obstacles for workplace optimization.
Aerial drones and unmanned aerial vehicles (UAVs) have become increasingly popular for tasks like inventory scanning in hard-to-reach areas. These devices can operate autonomously or can be remotely controlled by human operators, making them ideal for a variety of applications. Similarly, automated guided carts (AGCs) are designed specifically for transporting smaller loads within a warehouse or industrial setting. Meanwhile, automated storage and retrieval systems (AS/RS) offer efficient product retrieval using cranes or lifters on fixed tracks. Together, these automation solutions help businesses improve productivity and expedite their operations.
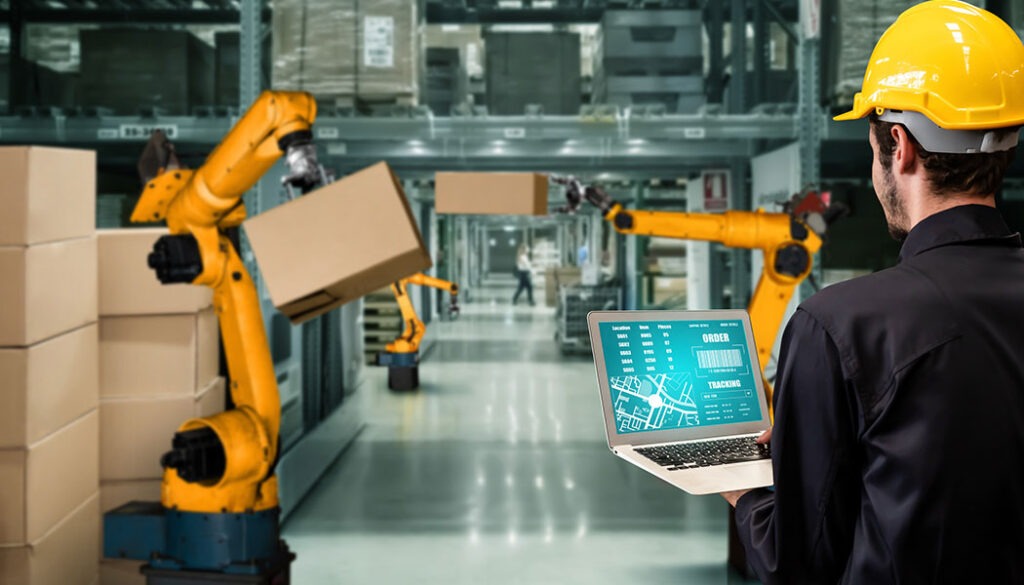
A warehouse robot in action
Collaborative Robots (Cobots), Articulated Robotic Arms, and Goods-to-Person (G2P) technology are all important tools in modernizing warehouse operations. These robots can work independently or with intervention to improve safety, efficiency, and productivity. Cobots follow or operate alongside humans, while articulated robotic arms are usually mounted on wheeled bases for mobility. G2P technology automates the delivery of goods to pick stations, making order fulfillment more efficient. Together, these types of robots are revolutionizing the way warehouses operate.
How embedded cameras help warehouse robots
Embedded cameras act as the eyes of warehouse robots, here are the different tasks camera modules help robots perform:
- Obstacle detection and avoidance: Depth cameras and LiDARs are used to measure the depth of nearby objects to detect any obstacle in their pathways.
- Localization and mapping: In areas where GPS is not available (so-called “GPS-denied” areas, such as inside buildings), robots use a technique called localization to find their position within the boundaries of the building or location. With the combination of 3D and 2D cameras, robots also create a 3D map of the surroundings. Some autonomous warehouse robots can use guided navigation with the help of barcodes (either laid on the floor or the warehouse walls and shelves) to move around.
- Object recognition: Images captured are interpreted using computer vision algorithms for robots to identify the exact objects to be picked from a cart or warehouse shelf and to enhance safety by distinguishing between human and objects.
How to select an embedded camera for warehouse robots
Selecting the right camera for warehouse robots involves understanding the role and importance of each specification:
Shutter type:
Global Shutter – When what needs to be captured moves fast, or if the vehicle is moving quickly, you may require a shutter type that captures the entire image simultaneously.
Rolling Shutter – The rolling shutter would be the better option otherwise as the camera costs are lower and are available in higher resolutions than global shutter cameras.
Also read: Global Shutter vs. Rolling Shutter in Embedded Vision
Resolution: For navigation, usually 5MP (or lower resolution) is sufficient as it provides enough detail without overburdening the system. The higher the resolution demand, the more processing power is required. However, higher resolutions may be necessary if the camera is used for reading complex text, barcodes, or QR codes.
Frame rate: To accurately capture and analyze the movements of fast-moving objects, it is important to have a frame rate that aligns with the navigation and control system goals. Greater than 30 fps provides smoother footage and more precise decision-making, but lower framerates may also work, depending on the control system requirements. Another consideration is motion blur, which can occur in cases where the exposure time is relatively long when compared to the motion of objects in the field of view and should be minimized as much as possible.
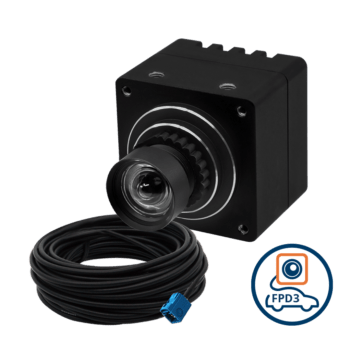
FPD-Link III Aluminium Enclosed Camera with onsemi AR0234 2MP Full-HD Global Shutter with Onboard ISP + S-mount Lens with IR-Cut Filter
VLS-FPD3-AR0234-SL
- onsemi AR0234 2.3MP Global Shutter Sensor
- S-Mount for Interchangeable Lenses
- FAKRA Z-Code Automotive Connector
- Plug & Play with Linux OS & Yocto
- VizionViewer™ configuration utility
- VizionSDK for custom development
Chroma: Monochrome cameras are preferred over color for tasks like barcode reading. This is because they offer higher sensitivity and are more effective in varying lighting conditions, ensuring consistent results. On the other hand, if the robotic vision system is required to capture color information such as color-encoded 2D codes, you must choose a color camera.
Related: Monochrome Camera vs. Color Camera: All You Need to Know.
Field of View: In certain cases, having a wider vertical field of view is crucial for better coverage. This can reduce or even eliminate blind spots, especially when fewer cameras are available. However, many product developers today prefer to use a higher number of cameras (placed at the head and the foot of the robot) to ensure the required field of view, along with the necessary resolution. As the field of view increases, the resolution required to discern detail at the required distance increases as well. Consequently, a higher number of lower resolution cameras with a smaller FOV can be a better solution than a lower number of higher resolution cameras with a wider FOV.
In addition to the vertical field of view, the horizontal field of view can also be important in certain cases. Inventory-tracking drones are a great example of this.
Depth capability: Stereo cameras utilize two cameras as a stereo pair to provide depth perception for tasks that require a 3D understanding of the environment including navigation and precise object handling, where accurate depth perception is crucial for success. Alternatives like time of flight or structured light cameras can also be used for depth perception.
Wrapping up
Warehouse automation is rapidly evolving with the emergence of robotics and AI, bringing promising changes to the industry, including increased efficiency, accuracy, and worker safety. At the forefront of this evolution is TechNexion – a leading provider of embedded camera solutions for warehouse automation. Our camera modules come with features such as a global shutter, high frame rate, NIR sensitivity, wide field of view, etc.
TechNexion is also a leader in embedded processing products for robotics. The ROVY family of compute modules, including ROVY-4VM and ROVY-4VH, help solve major problems by integrating vision processing, AI analytics, and real time control into a single compute system.
With a strong focus on innovation and reliability, TechNexion is an excellent choice for companies striving for success in vision-enabled warehouse automation. Learn more about our embedded vision and robotics solutions at www.technexion.com.